Milling
At present, the
Machining of large planes of cylinder blocks and cylinder heads in engines generally uses milling technology. Take the milling of a cast iron cylinder on a high-speed milling machining center as an example, using cubic boron nitride (CBN) inserts, and its cutting speed can reach 700-1500m/min.
The production efficiency of milling is greatly improved. For aluminum alloy cylinder heads, face milling cutters are used for high-speed cutting. Using PCD inserts, the diameter of the milling cutter is gradually reduced, and the development of multi-station compound processing.
Drilling
In the engine production process, the proportion of hole processing is also relatively high, especially the amount of hole processing for cylinder heads and cylinder blocks. Among them, drilling processing accounts for about 60%, followed by boring processing and tapping processing. Application of high-speed cutting tools
The history of the development of high-speed machining is the history of continuous advancement of tool materials. Most of the tools used by Shenzhen Ruiyihang Technology Co., Ltd. in the initial use of tools are imported, and breakthroughs have been made in localization. Now the more commonly used tools include CBN and PCD tools, coated carbide tools, ceramic tools, etc. . In addition, major breakthroughs have been made in the localization of quilting tools.
1. CBN and PCD tools
The representative tool materials for high-speed cutting are CBN and PCD. When using CBN tools for face milling, the cutting speed can reach 5000m/min. Machining the inner hole of 20CrMo5 hardened gear (60HRC) with CBN tool, the surface roughness can reach 0.22μm, which has become a new technology promoted by the automobile industry at home and abroad. Camshafts and crankshafts also use CBN grinding wheels for high-speed grinding; PCD tools are widely used in the milling of cylinder blocks and cylinder head aluminum alloy materials. Considering that high-speed rotation will generate a large centrifugal force, the tool body uses high strength Made of aluminum alloy material.
It is alumina grinding wheel. Because alumina base has high chemical stability and favorable thermal characteristics, considering practicability and economy, it is mainly used in the main journal cylindrical grinder with large grinding capacity, and the high-end grinding tool The representative CBN grinding wheel (see Figure 7) is applied to crankshaft connecting rod neck cylindrical grinders with higher follow-up requirements.
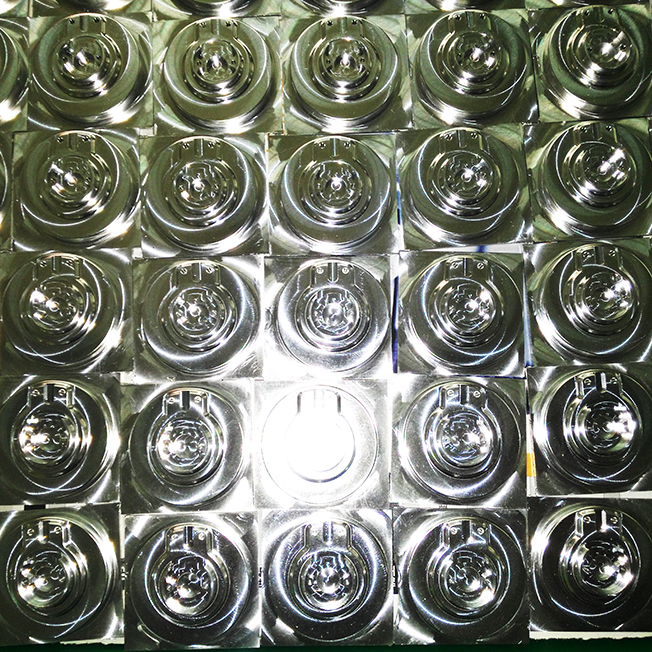
2. Carbide tool
Hard part cutting is an important application field of high-speed cutting technology. That is, single-edge or multi-edge tools are used to process hardened parts. It is more efficient than traditional grinding, and simplifies the process methods and links, which not only saves costs, but also More flexible.
In drilling and milling processing, ultra-fine grained cemented carbide is suitable for most applications. They also have high toughness and excellent heat resistance, which can combine favorable cutting edge geometries with large rake angles. And the clearance angle is integrated, the direct reflection of these characteristics is to reduce the cutting force and cutting temperature; when tapping, particularly high torque and elevated temperature at higher cutting speeds require very tough and high heat resistance Cutting materials.
3. Tool coating technology
In order to make cutting tools with low price and excellent performance, which can effectively reduce the processing cost, coating technology is currently the first choice.
The function of the tool coating: it can improve the wear resistance, increase the tool life, and improve the cutting performance; the existence of the coating reduces the friction between the tool and the chip, thereby increasing the drilling depth.
Reduce cutting force; bright coating appearance (golden yellow, fire red, etc.), easy to observe the wear of the tool; the presence of coating on the tool surface can reduce cutting heat and reduce the interaction of heat between the tool and the workpiece (coating isolation) The tool and the workpiece, prevent chemical reactions; the thermal conductivity difference between the coating and the tool can reduce the accumulation of heat on the tool); the high-quality coating can improve the performance of the tool and reduce the formation of built-up edges and crescent craters.
Comprehensive analysis of the economy and performance of the coating, the end mills used by Shenzhen Ruiyihang Technology Co., Ltd. for high-speed processing are mostly treated with TiAlN composite multi-layer coating technology, and the life of the drill bit with different coatings.