High-speed cutting is not only an increase in cutting speed, but also on the basis of comprehensive progress and further innovation in manufacturing technology, including major advances in driving, tool materials, coatings, tools, testing and safety, etc., in order to achieve cutting speed and advancement. Only by doubling the speed can the overall cutting efficiency of the manufacturing industry be significantly improved. The advantages of high-speed cutting technology are as follows:
1. Shorten production time
Using high-speed cutting processing, the cutting speed and feed rate are doubled, the overall cutting efficiency is significantly improved, and the processing time is significantly shortened.
2. Reduce manufacturing costs
Higher productivity levels will inevitably lead to a decline in manufacturing costs. The use of high-speed cutting equipment and tools can achieve the lowest manufacturing cost under mass production.
3. High-speed cutting absorbs energy
The use of high-speed cutting processing, on the one hand, reduces the heat generation of the workpiece during processing, especially in milling processing. Due to the reduction of heat generation, the workpiece heats up less, the
Machining size is stable, and the damage to the tools and equipment is also small; on the other hand, high-speed cutting can process hard materials, which is an advantage that ordinary machine tools cannot match.
4. Improve the processing quality of the workpiece
The use of high-speed cutting processing can greatly improve the processing accuracy and the quality of the cutting surface, and the surface roughness of the parts can reach the micron level, reducing and eliminating auxiliary work hours such as grinding and polishing.
High-speed machining in engine manufacturing
Nowadays, with the continuous adoption of new technology, the continuous development of superhard material cutting tools, coating cutting tools and alloy material cutting tools, high-speed machining has become more and more important in ordinary machining. Applications such as high-speed machining centers, high-speed external milling and high-speed grinding of CBN wheels in engine manufacturing are very common.
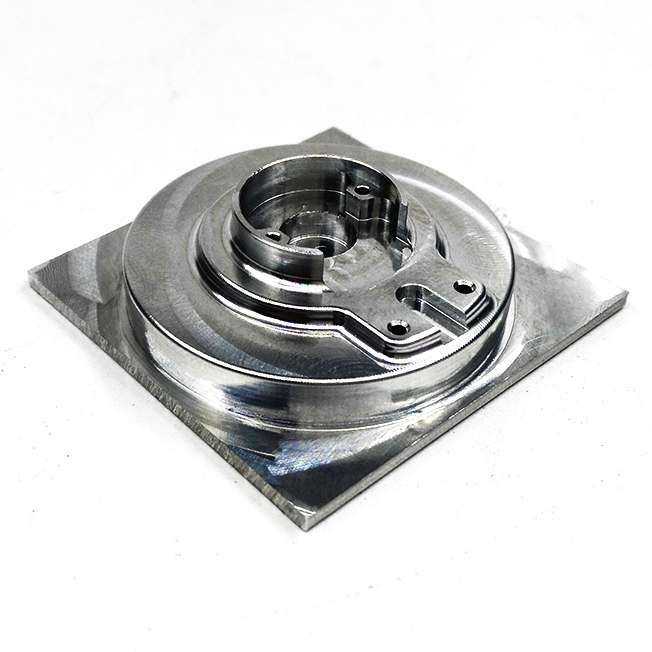
In the application of high-speed machining in the engine manufacturing industry, the main characteristics of high-speed spindles with electric spindles and high linear movement speeds with linear motors. The purpose is to replace multi-spindle machining centers with single-spindle machining centers with high spindle speed and high-speed linear feed motion It is difficult to realize a combined machine tool with high spindle speed and high-speed feed. The maximum speed of the spindle is generally up to 60000r/min, and the maximum feed speed is about 100m/min. The electric spindle incorporates many cutting-edge technologies, such as high-speed bearings that generally use composite ceramic materials or electromagnetic suspension, high-speed motor technology, timing and quantitative oil and gas lubrication, and automatic tool change devices. In order to reduce costs, some companies do not use linear motors, but use ball screws with hollow coolant, enlarged diameter and enlarged lead.
Shenzhen Ruiyihang Technology Co., Ltd. uses high-performance machine tools such as high-speed machining centers and CBN grinding wheels to achieve high-speed milling and grinding.