The main tools for processing stainless steel are stainless steel special milling cutters, stainless steel blades, stainless steel taps and drill bits, etc.
1. Features of stainless steel processing
According to the different organization of stainless steel at room temperature, stainless steel can be divided into ferritic stainless steel, martensitic stainless steel, austenitic stainless steel, and precipitation hardened stainless steel. And most of the stainless steel processed by the factory is mainly 201 stainless steel, 304 stainless steel and 316 stainless steel. 201 and 304 materials, with common carbide coated milling cutter, it is easy to process. And 316 material, or stainless steel contains more impurities and high hardness, you need to choose stainless steel special tools. The main features of stainless steel processing are as follows:
(1) Large cutting force
Compared with other difficult-to-cut materials, the strength and hardness of stainless steel are not high. However, when stainless steel is processed, its plasticity and toughness are good, high temperature, high strength, and serious work hardening.
(2) High cutting temperature
(3) Easy to stick to the knife and generate built-up edge
(4) Difficulty in chip breaking (not easy to curl and break when cutting)
(5) The tool is easy to wear
(6) Large linear expansion coefficient
2. What material tool should be selected for processing stainless steel?
For milling ordinary stainless steel materials such as 201 and 304, use ordinary carbide-coated milling cutters and choose 4 blades to mill well. Secondly, all major CNC tool suppliers have special stainless steel milling cutters. If customers are not sensitive to prices, they can choose this type of cutter.
When processing stainless steel, it is best to choose a material with high hardness, good wear resistance, strength and toughness, and good thermal conductivity.
Cemented carbide materials; YG and YW, etc.;
High-speed steel materials; W6Mo5Cr4V2Al, W10Mo4CrV3Al, etc.;
3. Reasonable cutting parameters for stainless steel processing
Stainless steel processing can be divided into rough
Machining and finishing. Rough machining can choose YW and YT cemented carbide with relatively low TiC content; for finishing, you can choose YW and YT cemented carbide with high TiC content. .
Secondly, in order to prevent edge chipping in processing stainless steel, the strength of the blade should be increased, and the rake angle is best to choose a smaller or negative value. If hard alloy is used for processing stainless steel, the helix angle is preferably 5-10 degrees. If high-speed steel end mills are used, 35-45 degrees should be selected. When milling stainless steel, it is best to choose an end mill with a larger helix angle, and when milling stainless steel pipes or thin-walled workpieces, you can choose a corn end mill.
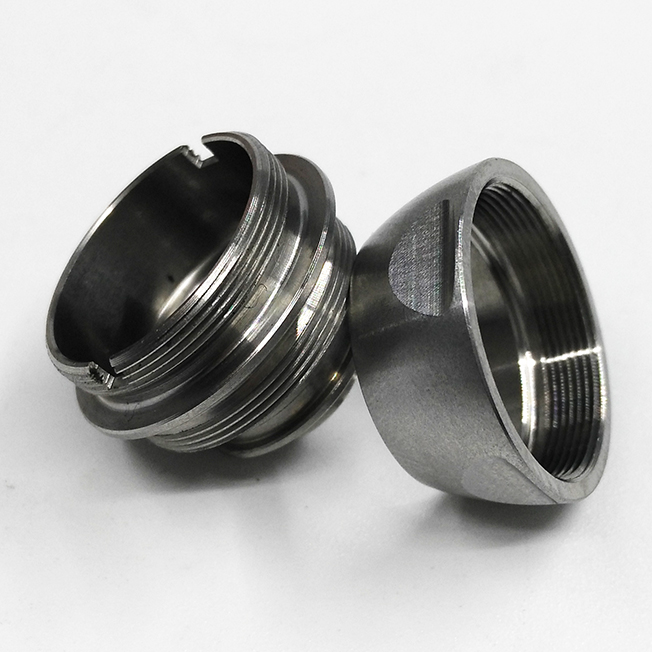
Commonly used stainless steel milling consumption;
Carbide end mills; cutting speed 10~140m/min; feed rate 0.013~0.15mm/z;
High-speed steel end mills; cutting speed 8~40m/min; feed rate 0.013~0.15mm/z;
Fourth, other knowledge of processing stainless steel
1. For processing high-hardness stainless steel, it is best not to use high-speed steel end mills;
2. If the hardness of the steel is higher, choose a lower milling amount;
3. When the amount of side tool is large, choose a lower milling speed;
4. Using coated carbide cutting tools, the milling speed can be increased by about 50%;
5. When cutting, pay attention to fully cooling off. If you use cemented carbide tools to process stainless steel, do not use water-soluble cutting fluids to avoid the cutting edge from being subjected to greater thermal stress and causing chipping.