CNC lathe processing is a high-tech processing method of precision hardware parts. Various types of materials can be processed, including 316, 304 stainless steel, carbon steel, alloy steel, alloy aluminum, zinc alloy, titanium alloy, copper, iron, plastic, acrylic, POM, UHWM and other raw materials, and can be processed into square and round combinations The complex structure of the parts.
Precautions for cnc processing:
1. When aligning the workpiece, only use the hand to move the chuck or open the lowest speed for alignment, not high-speed alignment.
2. When changing the rotation direction of the spindle, stop the spindle first, and do not change the rotation direction suddenly.
3. When loading and unloading the chuck, only turn the V-belt by hand to drive the spindle to rotate. It is absolutely forbidden to directly drive the machine tool to loosen or tighten it. At the same time, block wooden boards on the bed surface to prevent accidents.
4. The tool should not be installed too long, the gasket should be flat and the width should be the same as the width of the bottom of the tool.
5. It is not allowed to drive the reverse rotation method to brake the spindle rotation during work.
When we are processing stainless steel parts, we should all encounter the same problem: stainless steel parts are difficult to process; as everyone knows, the reason for the difficulty in processing is also the choice of tools. Let`s tell you what materials are used for the tools and how difficult it is to process stainless steel. Several reasons and solutions:
1. Turning stainless steel on automatic lathes, generally used carbide tool materials include: YG6, YG8, YT15, YT30, YW1, YW2 and other materials; commonly used high-speed steel knives include: W18Cr4V, W6M05Cr4V2AL and other materials.
2. The selection of the geometric angle and structure of the tool is also particularly important:
Rake angle: Generally, the rake angle of turning stainless steel tools is 10°~20°.
Relief angle: generally 5°~8° is more appropriate, *but 10°.
Blade inclination angle: generally choose λ to be -10°~30°.
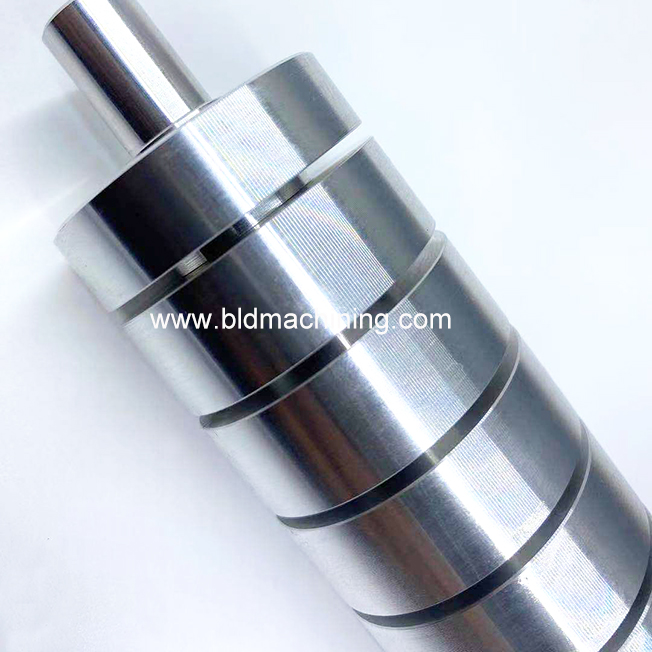
The surface roughness of the cutting edge should not be greater than Ra0.4 ~ Ra0.2.
3. There are several common difficulties in the processing of stainless steel parts:
1. The
Machining hardness causes the tool to wear quickly and it is difficult to remove chips.
2. Low thermal conductivity causes plastic deformation of the cutting pin blade and faster tool wear.
3. The built-up tumor is likely to cause small pieces of micro-chips to remain on the cutting pin edge and cause poor processing surfaces.
4. The chemical relationship between the tool and the processed material causes work hardening and low thermal conductivity of the processed material, which not only easily causes unusual wear, but also causes tool chipping and abnormal cracking.
4. The solutions to the processing difficulties are as follows:
1. Use tools with high thermal conductivity.
2. Sharp cutting edge edge: The chip breaker has a wider edge band, which can reduce the cutting pressure, so that the chip removal can be well controlled.
3. Appropriate cutting conditions: Improper processing conditions will reduce tool life.
4. Choose the appropriate tool: The stainless steel tool should have excellent toughness, and the cutting edge strength and the bonding force of the coating film should be relatively high.